There is a great need within all space programs to evaluate electrical and mechanical hardware during operation under various thermal conditions. Analysis is a critical tool during the early design of hardware but verification via physical testing is crucial. Electronic boards and motors become non-operational at low temperatures so the demonstration of adequate heating systems is required. MoonRanger will conduct such testing on several key subsystems, including the sensitive wheel modules and avionics enclosures.
Emulating the lunar south pole’s ultra-cold, ultra-high vacuum environment here on Earth requires a cryogenic vacuum chamber. Printed circuit boards (PCBs), actuators, and other test articles must be tested to verify their performance in a space-like environment. Removal of all air within the vacuum chamber deprives test articles of heat transfer by means of convection, as would be experienced on the moon. Within this gas-free environment, thermal conditions akin to the lunar surface must be imposed.
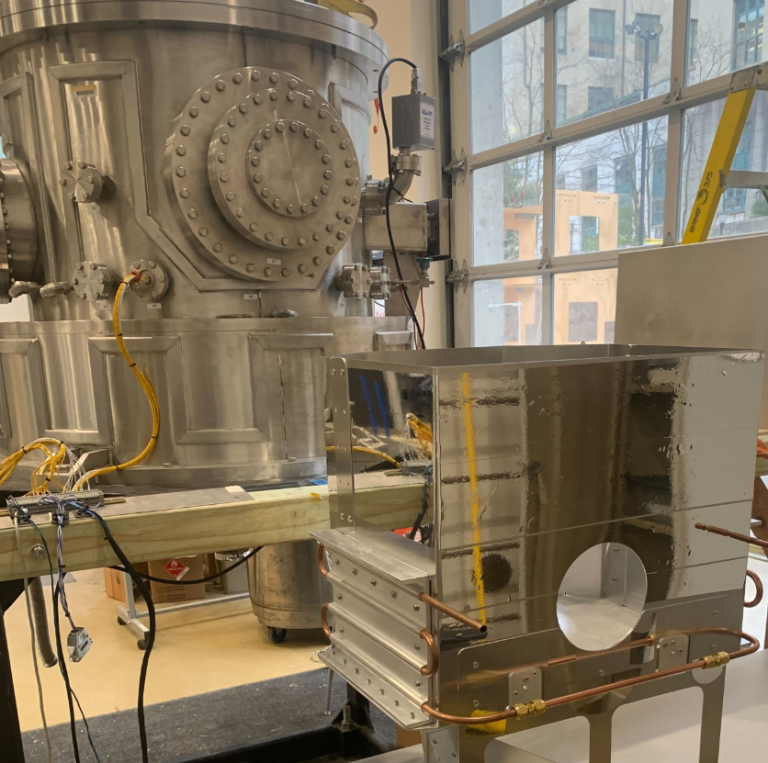
Thermal extrema cannot be easily reproduced in the lab environment without specialized hardware. The most practical approach to achieving controlled temperatures below -150° Celsius is to employ liquid nitrogen as the working fluid in a thermal exchange system. Within a vacuum, heat from the object under test is radiated to a large metallic structure and extracted from the system via the flow of liquid nitrogen. This large shroud was built from bent 5052 aluminum, fabricated and assembled in-house. LN2 (liquid nitrogen) enters the vacuum chamber and travels through a winding path of copper tubing. The tubing passes through several aluminum heat exchange plates which make good thermal contact with the larger aluminum shroud. The aluminum shroud is covered externally with highly reflective thermal control films which prevent the heat of the vacuum chamber from radiating onto the shroud. LN2 is amenable for this application as it’s boiling temperature is -196° Celsius. Heat from the article under test is absorbed into the working fluid and vaporizes a small portion. This allows a system using LN2 to quickly achieve temperatures approaching -190° Celsius. Additionally, the system can be controlled at any specified temperature by adjusting the amount of LN2 that is permitted to flow through the system. The flow of LN2 is adjusted using an on-off solenoid valve, the position of which is activated using a rudimentary bang-bang control scheme similar to that of a residential thermostat.
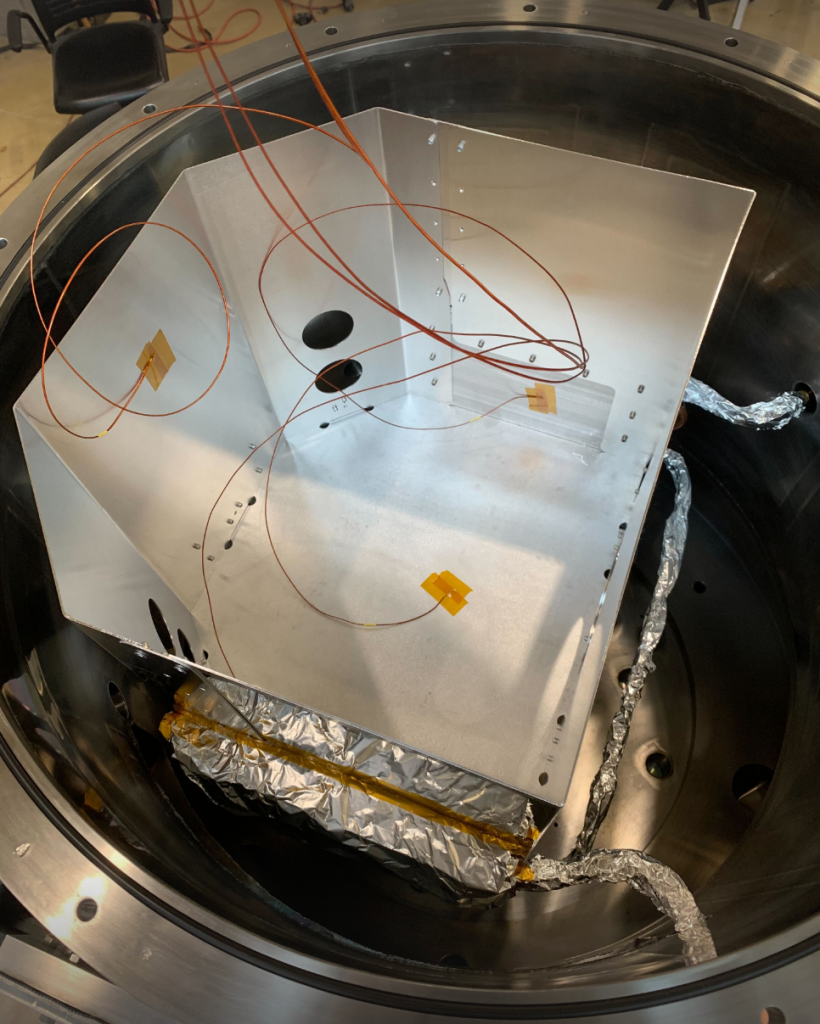
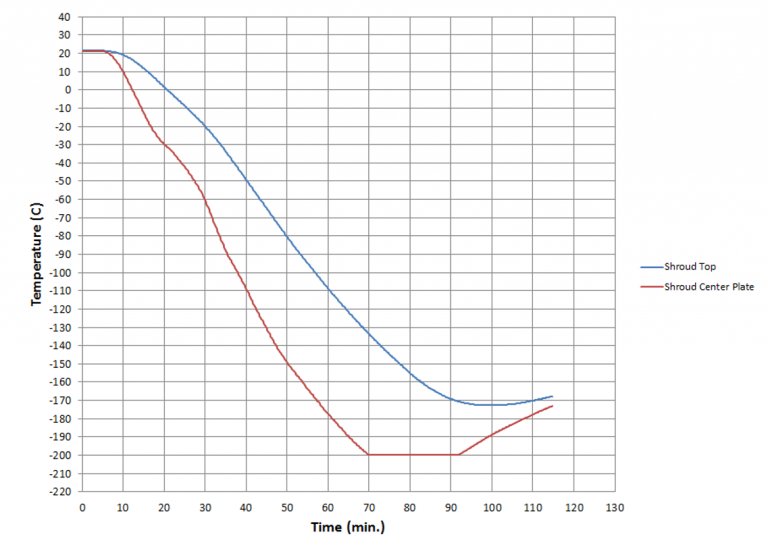