One of the great distinctions of space robotics versus terrestrial robotics is that every component, device, sensor and electronic element has to function in vacuum. Once in vacuum, Earth’s convection due to air circulation no longer exists, so regulation of heating and cooling in a space system relies on the far weaker mechanism of radiation, so it is far more challenging than terrestrial counterparts. When vacuum and thermal are tested together, the apparatus and process are connoted TVAC — Thermal/Vacuum.
The body of CMU’s TVAC system is an airtight chamber that is 30 inches diameter and 30 inches deep. We initially procured it without pumps, data acquisition apparatus or wire pass-throughs from Ebay. In order to decrease convective heat transfer to a negligible level the vacuum chamber must achieve a pressure of 5E-4 Torr or less. At this pressure, there is 1,500,000x less air in the chamber than at atmospheric pressure. Attaining such low pressure is not a simple feat. This chamber primarily utilizes “Conflat” all-metal seals that close by crushing an annealed copper gasket between two sharp stainless steel knife-edges to form a molecularly perfect seal. A moderate vacuum of 5E-2 is first achieved by a high-volume Alcatel 2004A (3.2 cfm) rotary ‘roughing pump’ in about 20 minutes. The 5E-4 is then achieved by an Alcatel 5081 (80 l/s) turbopump in about 10 more minutes.
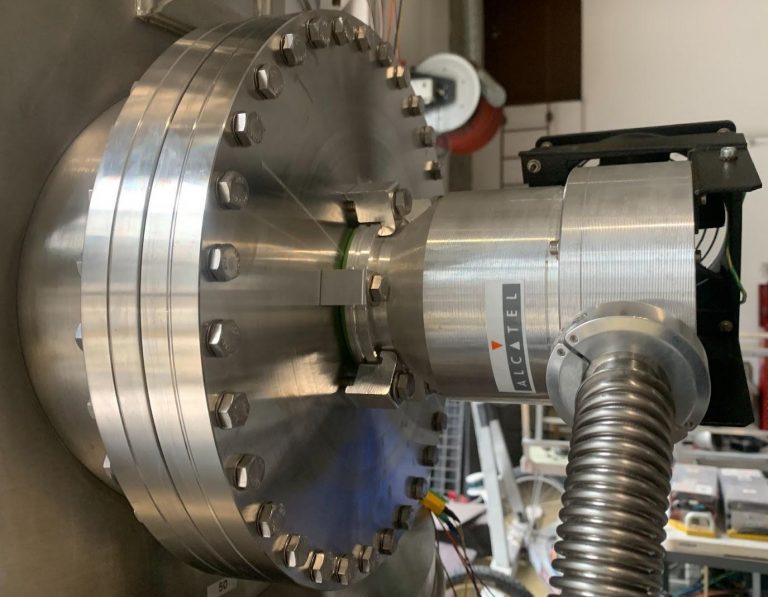
The turbopump is mounted directly into the side of the chamber to prevent restriction of the inlet diameter and minimize the flow path length. At low pressures, molecules of air are no longer governed by viscous forces and must “random-walk” their way into the inlet of the turbopump. By minimizing the path length that the molecules must travel, the pumping rate is significantly improved. Better pumping and a shorter pump-down time allows more tests to be conducted in a single day.
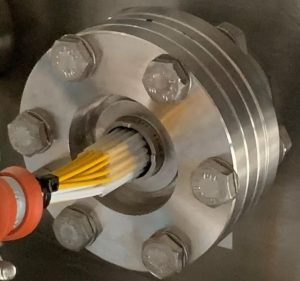
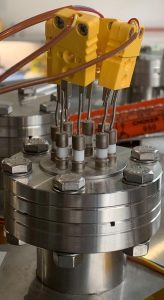
Electrical and fluid connections into the chamber are provided using vacuum “feedthroughs”. These components consist of a standard conflat vacuum flange that allows wires or pipes to pass into the chamber without breaking the seal to the outside. The hermetic connection is made by brazing alumina ceramic or melting glass around the wires to seal and electrically isolate them.
Simulating a Space Environment
Within the chamber, hardware can experience a near space-like environment and be pushed to thermal hot and cold extremes. The system has accommodations for simultaneous heating and cooling. Heating is accomplished by an internal xenon lamp capable of providing 40 watts of heat via radiation onto the test article. The maximum achievable temperature within the system is around 160° C. To achieve cold temperatures an aluminum/copper cold plate is fed cryogenic liquid nitrogen (LN2). The temperature of the plate is monitored using several thermocouples and the flow rate of LN2 is modulated using a solenoid valve and a PID control scheme. This enables the TVAC system to achieve cold temperatures approaching -190° C.
Depending on the type of test we are running, the boundary conditions can be adjusted to accurately match the expected space environment. For example, when investigating the thermal isolation of Moonranger’s wheel modules assembly, we place the outer wheel rim in direct conductive contact with the cryogenic cold plate to simulate contact with cold lunar regolith while driving on the moon. For other tests, when only investigating radiative heat transfer effects, we suspend the test article above the cold plate so that it has negligible conduction pathways.