Thermal vacuum testing of components and assemblies is essential during the design, prototyping, and pre-integration of a Moon rover to ensure that its electronics and materials will operate at the pole of the Moon, where temperatures can swing 250 degrees from hot to cold, but electronic temperatures must be moderate. This requires a chamber that can generate the vacuum and heating and cooling to test the components over their operating ranges. Data collected is essential to the project, as the tested performance takes precedence over all theoretical analyses and simulations that have gone before.
In-house testing enables the team to make necessary changes to the rover. The in-house testing results impact design decisions and reduce the chance of any unwelcome surprises during full system tests. Since this kind of testing involves small, frequent experiments for all crucial components, it is an integral, proactive step before assembly begins.
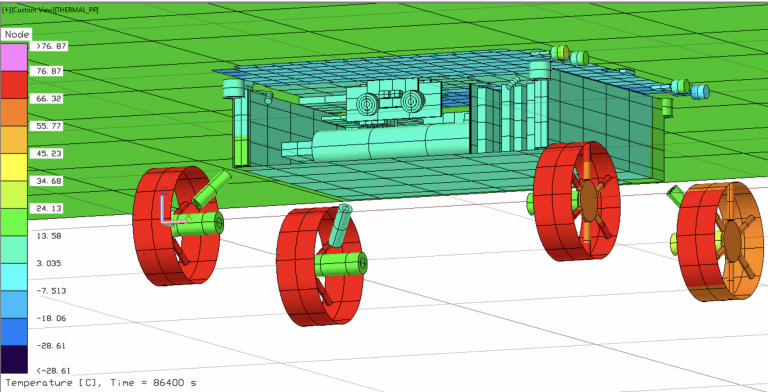
In-house vacuum testing aims to verify the conductance of thermal interfaces. Conductance (W/K) is conductivity times area divided by material thickness and is the standard measurement for quality interfaces (i.e. high conductance is good, low is bad). If the conductance is too low, then this informs further design considerations and implementation.
All components are tested in the vacuum chamber, a tightly sealed stainless steel container that can be evacuated of air by vacuum pumps. On the high end, the test plate can reach 160° by an internal xenon lamp capable of providing 40 watts of heat via radiation. Resistive spot heating is added to some components to simulate heat that electronics might generate. Liquid nitrogen (-190°) can be circulated through a cold plate to cool experiments. Temperatures during an experiment are tracked by thermocouples monitored by a digital acquisition system. The concurrently imposed radiative heating, cooling, and spot heating emulate the conditions encountered on the Moon to high fidelity. The chamber, pumps, xenon lamp, nitrogen cooling, spot heating, and data acquisition modules comprise the vacuum and thermal system (TVAC).
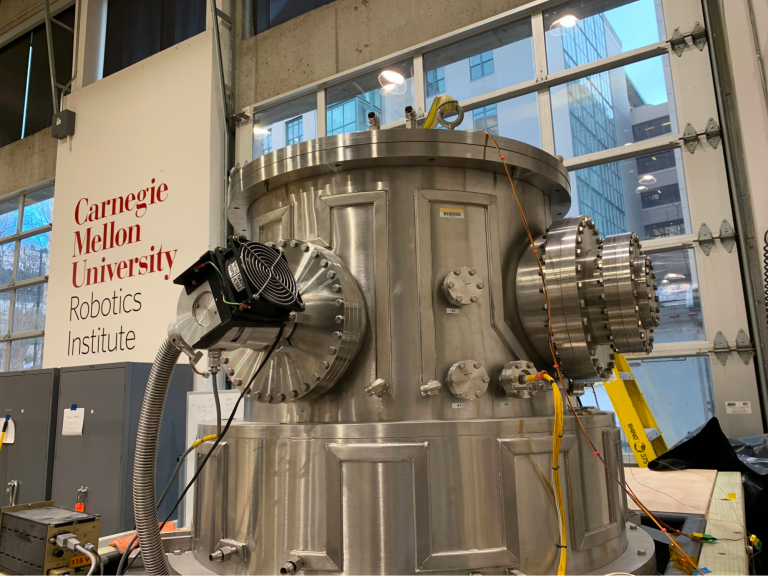
Depending on the type of test, the team can adjust conditions to match the expected space environment. For example, when investigating the thermal isolation of Moonranger’s wheel modules assembly, we place the outer wheel rim in direct conductive contact with the cryogenic cold plate to simulate contact with cold lunar regolith while driving on the moon. For other tests, when only investigating radiative heat transfer effects, we suspend the test article above the cold plate so that conduction is negligible and all transfer is radiative.
Interviewed: Paulo Fisch
Technical Writer: Kerry Mills, Kevin Fang