During the mission, MoonRanger’s bolted connections are subject to tensile, shear, thermal loads, and the effects of vibration and creep. The desired initial tensioning of the bolt is computed based on these factors. Determining and implementing the correct torque for each bolt on a space robot is essential engineering, process and discipline. Connectors for a space robot are small, strong, stainless steel. Many of these thread into and connect aluminum. Aluminum is much weaker than steel, so over tightening the bolts damages the (irreplaceable) aluminum threads and reduces the strength of the connection. This precision assembly happens once, and there is no margin whatever for error. If under tightened, the bolts preload will be too low and performance of the joint in both tension and shear will be reduced. The torque level initially set must also consider changes in joint tension when it is stressed, such as by shaking during launch. In addition to structural loads, differential thermal expansion of the bolt relative to the materials clamped by it induces strain in the joint. Given the temperature extremes experienced in space, this thermal loading is non-negligible. All of these factors must be considered when determining the installation torque of a fastener.
TWISTR
The TWISTR (Torque With Integrated Simultaneous Tension Reading) test apparatus is used to determine how much torque is required to generate the desired level of tension on each type of bolt for each of the robot’s connections. This experimental result is used in conjunction with theoretical analysis to determine installation torque specifications for flight hardware. The torque threshold and sensitivity of the device can be used on fasteners as tiny as #2-56, and as large as ¼-28 in size.
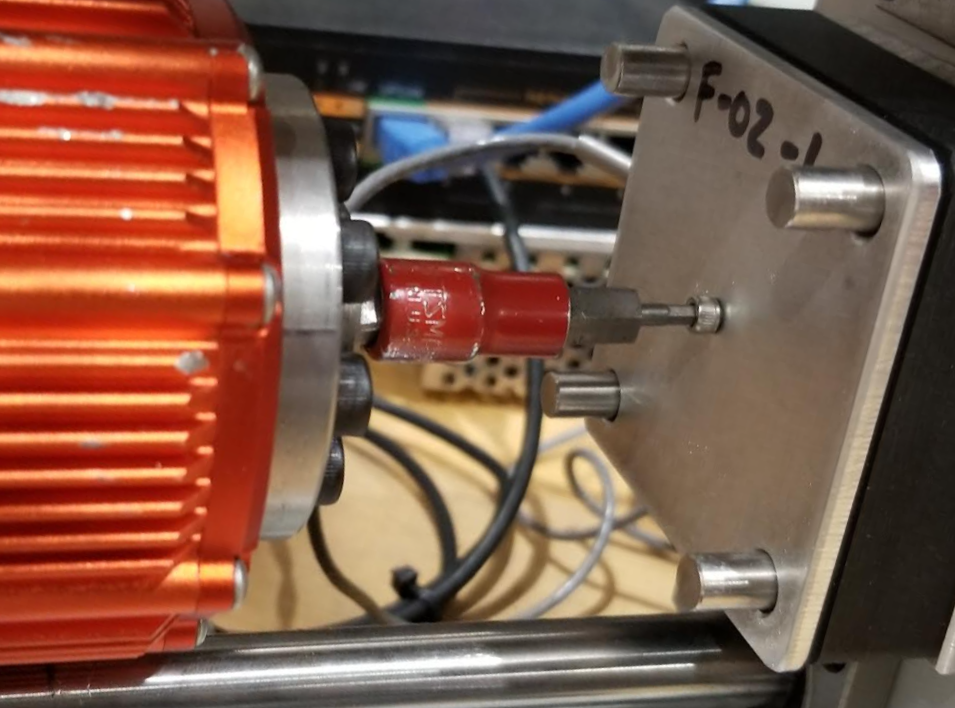
TWISTR applies a known amount of torque using a series-elastic actuator, which tightens a bolt on a load cell (hidden within the black plastic layer) to measure the resulting tension. All data is recorded by a data acquisition system.
The most important factor for bolt torque is the friction factor within the joint. A collection of material plates were fabricated. These plates can be stacked in any combination to accurately represent the material make-up of any joint on the robot.
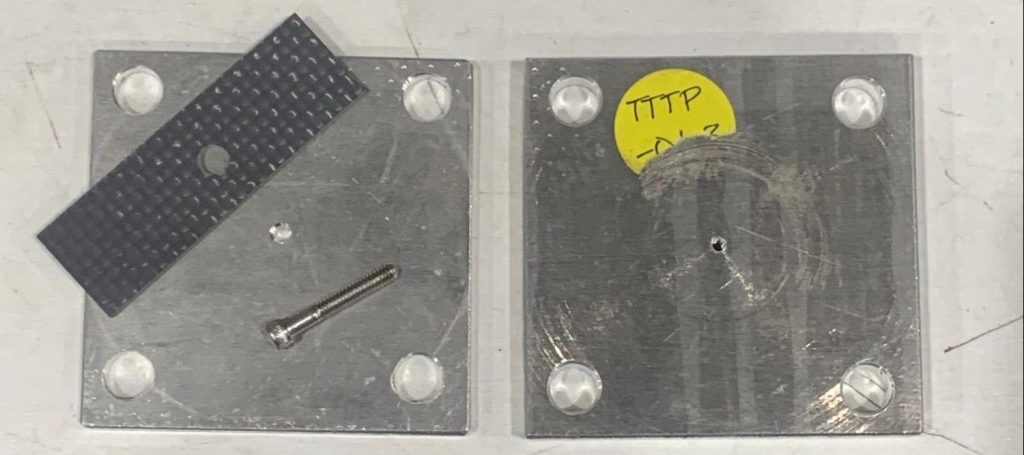
The device is controlled by a custom Matlab interface. After collection, the data is automatically processed by the program. There are generally four distinct phases of fastener installation, as visible in the data plot on the left. First, prior to clamping, there is a non-zero “running torque” that results from the friction of the fastener in the threaded hole. MoonRanger uses many “distorted thread helicoils” that intentionally increase the running torque to prevent the fasteners from loosening when they are vibrated. The second phase is “elastic tightening”, visible as the first sharp rise in tension. This indicates that the bolt is now clamping the joint tightly. A correctly designed joint should operate exclusively in this regime. Thirdly comes plastic deformation of the bolt or threaded hole, indicated by the sharp decrease in slope on the data plot. At this point, the bolt or threaded hole is being permanently stretched and damaged. Lastly comes the sharp drop in bolt tension, indicating that the bolt has fractured. At this point the bolt provides zero clamping and the joint is non-functional.