MoonRanger’s carbon fiber composite chassis shell was a triumph of design, process and master craft. Although metal design and machining is much more straightforward, only a composite solution was sufficiently lightweight. A campaign of design, facility development, mold-making, process development, layup, curing and machining created this elegant structural element. The 18” x 17” x 4” stiff, strong flight shell weighs only 820 grams.
The Layup Stage
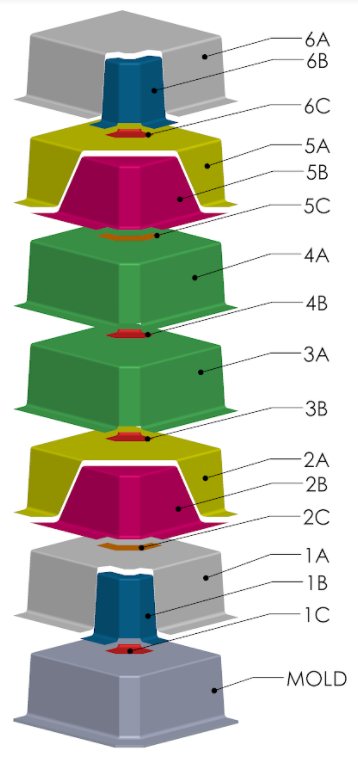
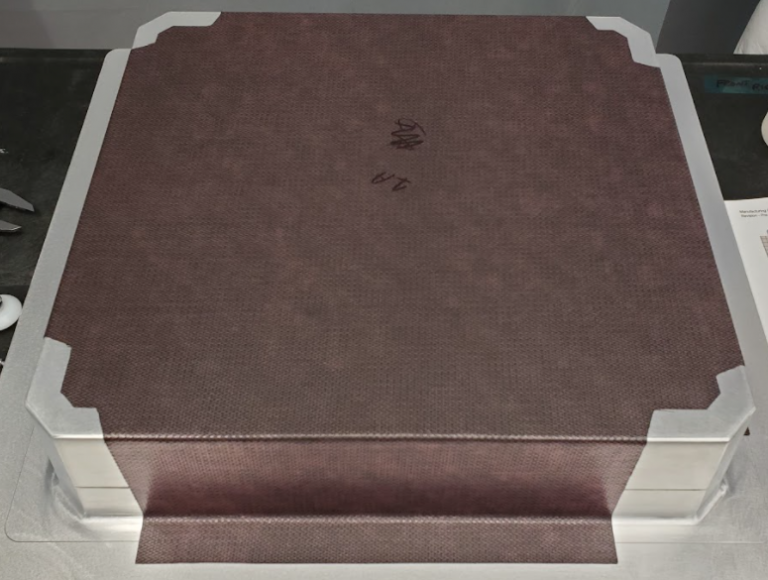
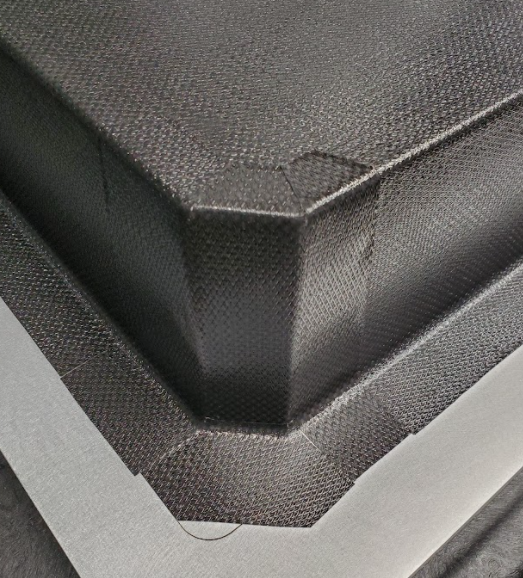
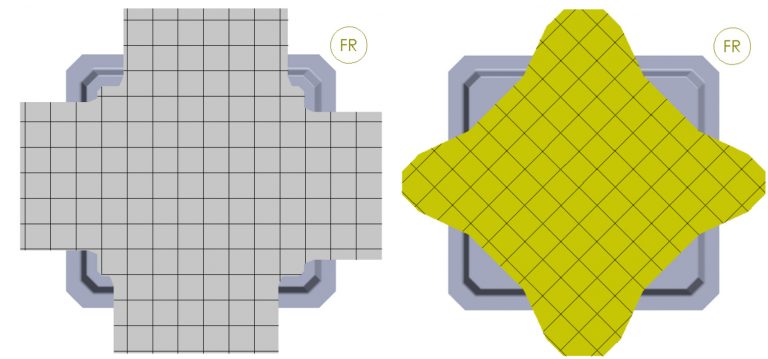
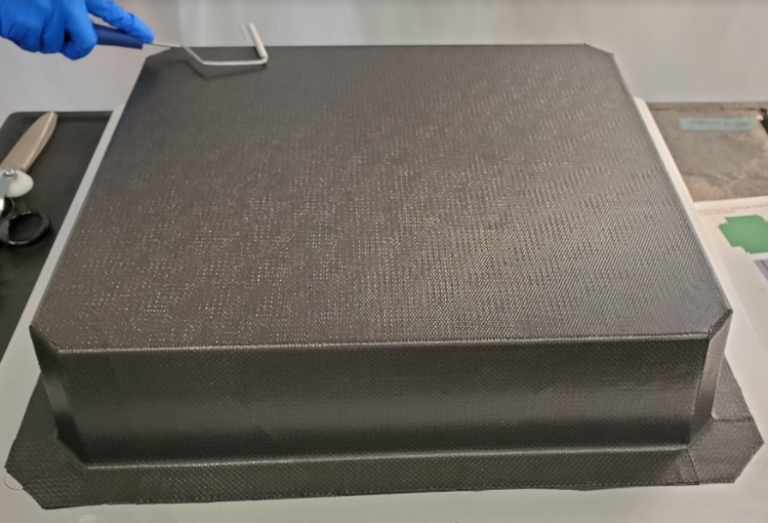
A Vacuum Environment
The layup is cured under vacuum. The technique utilizes atmospheric pressure to evenly press the composite layers against the mold. Several layers of material are introduced between the composite laminate and the vacuum bag. Breather fabric facilitates air evacuation while pulling vacuum, caul plates are used to ensure flat faces of the shell are clamped evenly, and release film inhibits bonding between the laminate and the aforementioned layers. The mold, shell, and aiding layers are placed inside a vacuum bag. Note that the layup and curing occur in a temperature and humidity controlled clean room environment. Under vacuum, all layers are squeezed against the mold. The unit (still under vacuum) is partially cured in an oven, followed by complete cure in an autoclave. The autoclave is pressurized to several atmospheres, offering a multi-fold increase in clamping force beyond what is possible by vacuum alone.
The shell is trimmed to remove excess material around the edge. Later machining introduces pass-thru cutouts and mounting holes.