Design and Fabrication of Foam Hands
We present a novel class of tendon-actuated soft robots, which promise to be low-cost and accessible to nonexperts. The primary structure of the robot consists of flexible foam, and so we term the robots created using our approach “foam robots.” A foam robot moves by driving servo mounted winches that contract (or slacken) tendons routed through the robots textile skin. We provide a methodology for fabricating these types of robots and go on to fabricate several ‘foam robots’ in the form of multi-fingered hands and perform various experiments and demonstrations to illustrate the robust applications of these robots to tasks such as dexterous manipulation.
See the associated paper! (Best Interactive Paper – Finalist, IEEE Humanoids 2018)
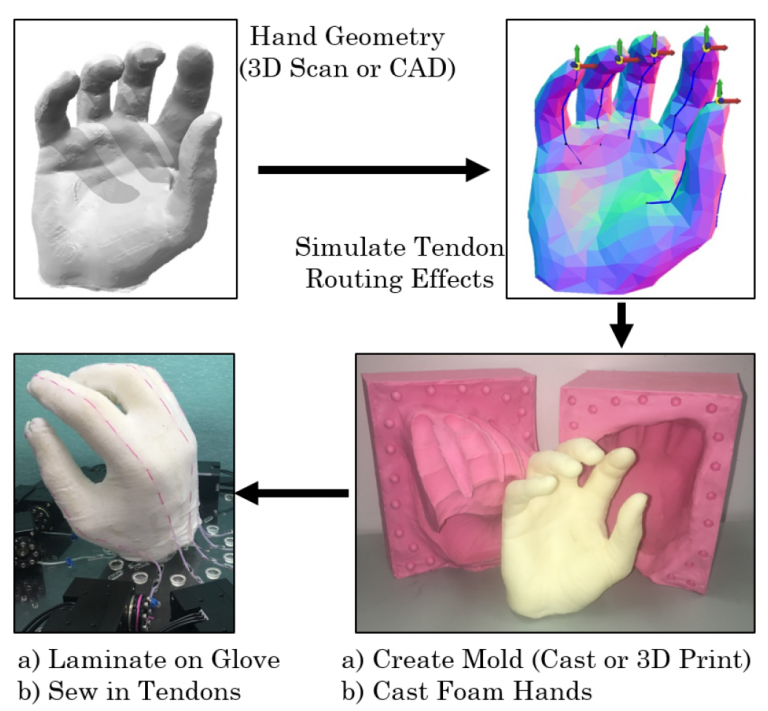
Creating the Mold
An initial hand pose is chosen and evaluated in simulation to find tendon networks that result in the ability to achieve desired poses. If necessary, the user iteratively changes the hand geometry to better suit their tasks. Using the hand geometry the user can either use CAD software or automatic mold generation methods to yield models that can be 3D-printed or machined. Additionally, the mold can be made by casting physical objects, such as a real human hand.
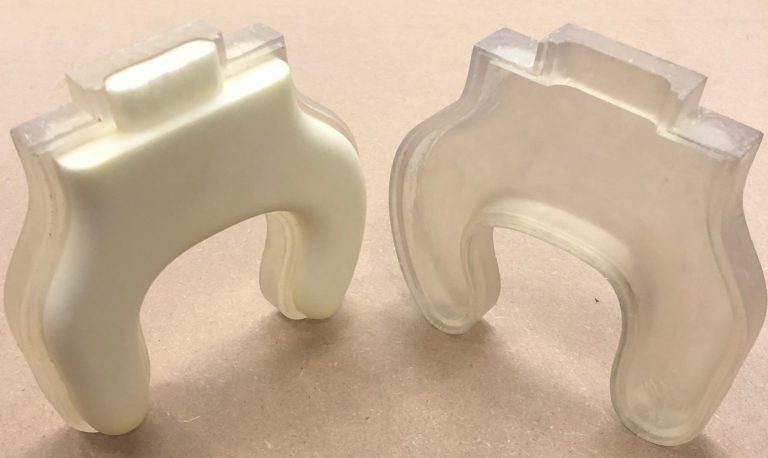
Casting the Hands
A two-part urethane foam compound is used to cast the final foam hand, a mold and cast of a planar two-fingered gripper is shown in the figure above. A variety of densities are available to choose from that best match the user’s application, we most preferred FlexFoam-iT! X, finding it a good balance of strength and compliance. The behavior of the foam is not always intuitive: while casting humanlike hands we found that slightly thicker sections of the palm were much stiffer, and slightly thinner sections of the fingers were much softer. Therefore, the hand geometry should be carefully considered to avoid unwanted behavior. While not necessary, the use of a laboratory mixing machine guarantees very consistent results from cast to cast.
Of great benefit is the ability to go from a chosen rest pose or model to a cast foam hand in under 24 hours for a cost of a approximately $50 for the mold and only a few dollars for each foam hand afterward. The ability to make a large supply of foam hands in a time and cost efficient manner is very important for lowering the barrier to entry for researchers desiring to experiment with soft robots.
Gloves and Tendons
A textile exterior, e.g. a glove, is used as a skin for the foam hand, acting as a layer conducive to sewing in tendons for actuation. For anthropomorphic hands, off the shelf gloves can be used, but for general soft robots, sewn skins from cut felt can be used. In our case, gloves were custom knit for each hand geometry by way of automatic processes. The custom gloves can be knit in under an hour with many choices of materials, greatly complementing our rapid prototyping approach. Whatever choice of skin is selected, it is then laminated to the foam core to prevent slip using spray-on upholstery adhesive.
Tendons are realized in practice with PTFE coated braided fishing line, and are sewn into the glove with a typical sewing needle, and fixed at the ends with finishing knots.
Wrist/Chassis
The gloved hand is fixtured to a laser-cut acrylic base with hot-melt glue. The tendons are routed through PTFE tubes along the base of the hand to minimize friction where they then interface with servo driven winches. Additional mounting points are placed on the acrylic base so that the PTFE tubes can be fixtured with cable ties. The assembly is detailed in the image below.
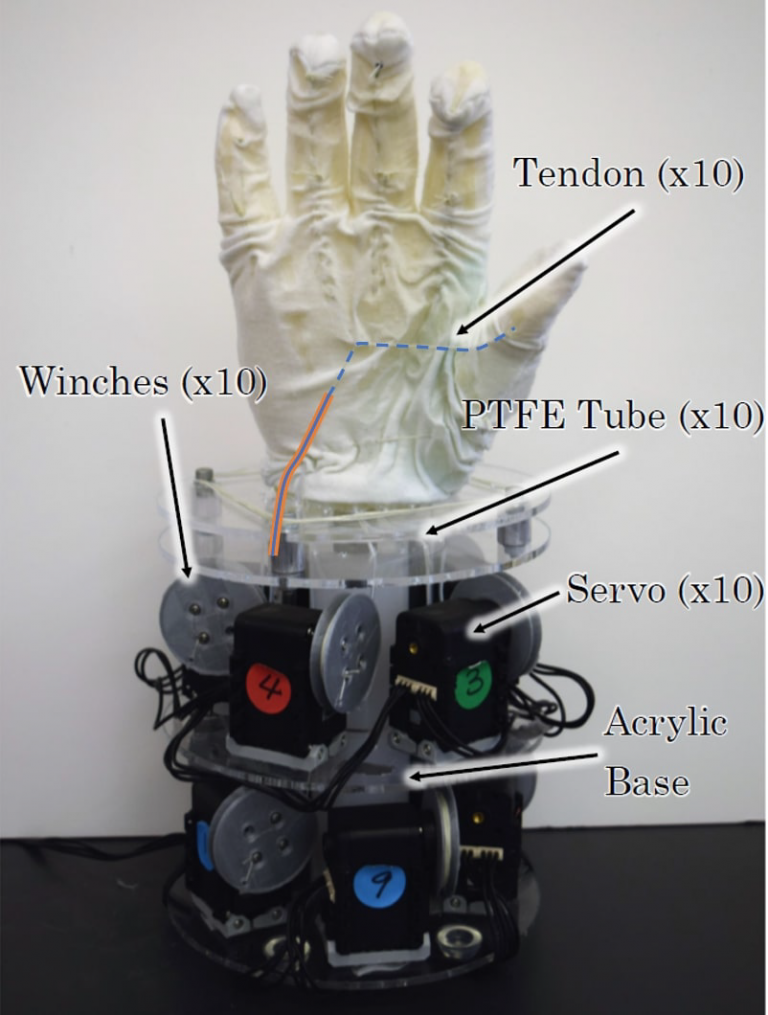
Publications
J. P. King, D. Bauer, C. Schlagenhauf, K-H Chang, D. Moro, N. S. Pollard, and S. Coros, 2018. Design, Fabrication, and Evaluation of Tendon-Driven Multi-Fingered Foam Hands, IEEE-RAS International Conference on Humanoid Robotics (Humanoids), Beijing, China, November 2018.